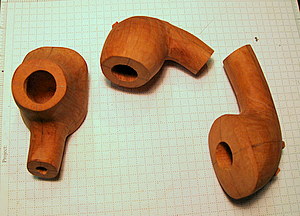
When we last saw our hero he had bravely roughed in and freehand drilled three stummels, as seen here on the right.
Now it’s time to rough in stems to go with these stummels before we dive into refining the shape. I do as much of the shaping process with stems and stummels together, which contributes to the aesthetic flow of the pipe, as well as ensures a good mating of shank and stem.
I hand cut all my stems– it takes time, lots of time, but it pays huge dividends in smoking properties, as well as aesthetics. I use either German Ebonite or Cumberland rod, a bit pricey, but well worth the expense. Unlike Lucite, high quality German Ebonite and Cumberland feels great on teeth and does not taste of plastic. It also avoids the rubbery taste and tendency to oxidize that pre-molded stems have. It also machines and shapes extremely well, and looks fantastic when polished up.
I’ll sometimes use exotic materials for inserts, and you’ll see boxwood in the first stem attempt for the Volcano which appears in the pictures (more on why I had to make 5 stems for three pipes latter ;(.
My initial design for the Volcano used a boxwood insert with a Delrin Tenon. These days I hand cut most of my tenons from the stem material itself (you’ll learn way later), but on some designs prefer to use Delrin. The following is the procedure I use when combining a Delrin tenon with exotic insert materials.
I like to leave the stem material in the lathe for the entire process (glue up and drilling). This prevents having to re-center it for drilling operations. Multiple sessions where the stem is in and out of the lathe can introduce problems, even with the self-centering chuck I have for the stem lathe.
First I prepare the stem material in the lathe by roughing in the diameter of the stem rod, turning it down to the maximum diameter). Then I face the with a Forstner bit:
The diameter of the Delrin used for the tenon will largely depend on the pipe’s final stem and shank diameter. It is critical that the drills match the Delrin I’m using, especially with regard to the fit of the tenon in the stummel mortise. Both drills and Delrin very slightly, so some experimentation with speed, feed rate, and different drills, even of the same marked size will result it the best fit. Once I find a good drill, I keep track of it. It’s sometimes advantageous to use a different drill for the stummel than the one used for the stem material.
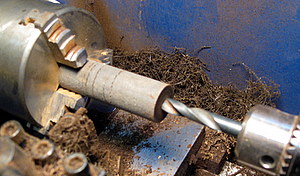
Next I prepare the inserts by slicing sections of the material to be used for the cap and insert material(s).
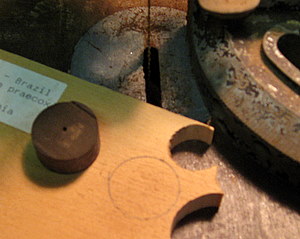
They must be thicknessed and flattened so they fit perfectly together without any gaps or voids. This can be done by sanding on both sides with sandpaper backed against a good flat surface (the top of a flat work bench works, but a thick piece of glass, granite, or marble would would be better).
Care must be taken the sides of the slices are parallel. This can be checked with calipers. You can leave the outside cap material thicker and do not need to worry about the outside surface which will mate with the stummel. It will be finished by facing it off with the lathe after its glued up, which insures a good fit to the shank, and also allows for tweaking the design aesthetically by adjusting its final thickness. Insure the insert and stem materials are completely flat and fit together without any gaps or voids between them. Then, while keeping the material together as it will be glued up, drill a slightly oversize hole hole through the center of them using a drill press (using 1/64″ oversize drill allows the materials to fit flat against the main stem and each other by avoiding the possibility of binding on the tenon).
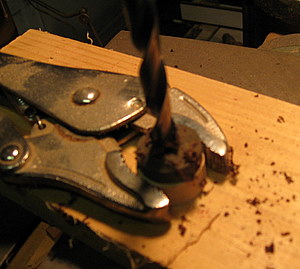
Next I measure and cut the section of Delrin to be used, making sure you leave extra length to allow for trimming it to perfectly match the depth of the mortise. Here I’m also gluing up insert material, so that is also accounted for in the length:
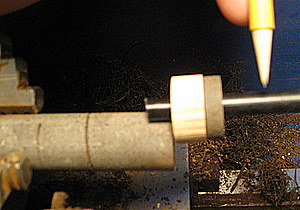
I round the end of the Delrin to match the bottom of the hole drilled in the stem material. This will minimise any voids and pockets of epoxy:
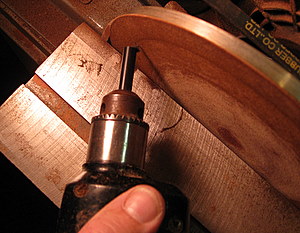
First I dry fit everything to ensure your fit is good:
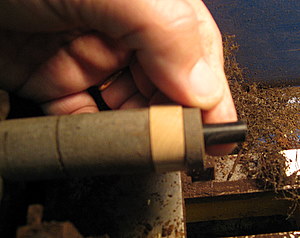
It’s essential when using Delrin to rough up both surfaces (the Delrin, and the hole in your stem material). This will greatly improve the bond between the two materials:
Then I mix up epoxy and coat both surfaces of both the hole of the stem and the end of the Delrin (as well as both surfaces of any insert material being used):
I use a thin even film of epoxy. Rotate and press all the materials against each other to release any air bubbles and squeeze out any extra epoxy:
I carefully wipe away any squeeze out off of the tenon (the squeeze out around and insert materials can be easily trimmed when it’s dry, but the tenon should stay as clean as possible). Then I use the trimming tool in the cross carriage of the lathe to press the insert materials against the main stem and to each other and lock it into position. I use the drill bit chucked into the tail stock to press the Delrin firmly into the stem while the epoxy sets, and lock it into position.
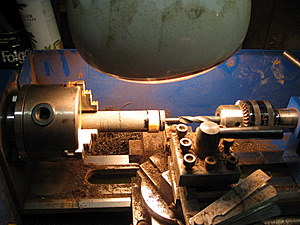
These serve as excellent clamps. I let all this sit overnight. During cold or damp weather I leave the light down close over the assembly (as shown above) while the epoxy is curing.
Next comes trimming up the stem inserts to match the rest of the stem, or start rough shaping to the intended design for them. Once getting the tool carriage and tail stock out of the way I rough trim the insert materials by hand with a coarse file or fine saw until they are round enough not to catch while turning, then spin up the lathe and trim and sand the inserts flush with a good sharp HSS cutting tool and sandpaper. If the design accommodates planning ahead at this stage, I work toward getting close to the thickness I want for the stem/shank joint, or any other part of the design that will benefit from being turned.
Next I trim the end cap to the desired thickness and face it off so the surface will be fit flush against the stummel.
At this point I can now fit the length of the Delrin tenon to the mortise. This and drilling are the same I procedure I use as when I have cut an integral tenon into the stem material. I first bevel the tenon so it will not damage the mortise in the stummel, then check the stummel and measure how much to trim off the tenon:
Next I transfer the measurement to the stummel and trim the Delrin:
Next I bevel the tenon again, and recheck that I have it correctly fit to the mortise: